SEPARATION OF THE POLYMER MASS FROM THE WASTE OF THE ALKALINE CLEANING PROCESS OF PYROGAS BY THE EXTRACTION METHOD
DOI:
https://doi.org/10.61151/stjniet.v8i4.349Ключевые слова:
polymer mass, hydrocarbon content, yellow oil, solvent, extraction, organic extractant, alkaline water, selective extractant, raffinate, extractАннотация
Abstract:
Objective. Pyrogas treatment waste segregation and consists in choosing a selective extractant to extract the polymer mass from the hydrocarbon content.
Methods. Segregation of waste, determining the solubility of hydrocarbon content in various solvents and methods such as choosing the most optimal selective extractant for extraction were used.
Results. The waste is separated into two layers when it is cooled. 1 - the upper layer (light layer) is determined to be "hydrocarbon content" and 2 - the lower layer (heavy layer) is "alkaline water". Paraffin hydrocarbons have been proven to be the best extractants for separating polymer mass from hydrocarbon content. The molecular mass and density of paraffin hydrocarbons have been found to have an inversely proportional effect on the separation rate of extract and raffinate during the extraction of hydrocarbon content.
Conclusion. It was found that the most effective method of separating hydrocarbon content and alkaline water from the waste is the leaching method, and the time of leaching is 240 minutes. Paraffin hydrocarbons were selected as an extractant for the extraction of polymer mass from hydrocarbon content.
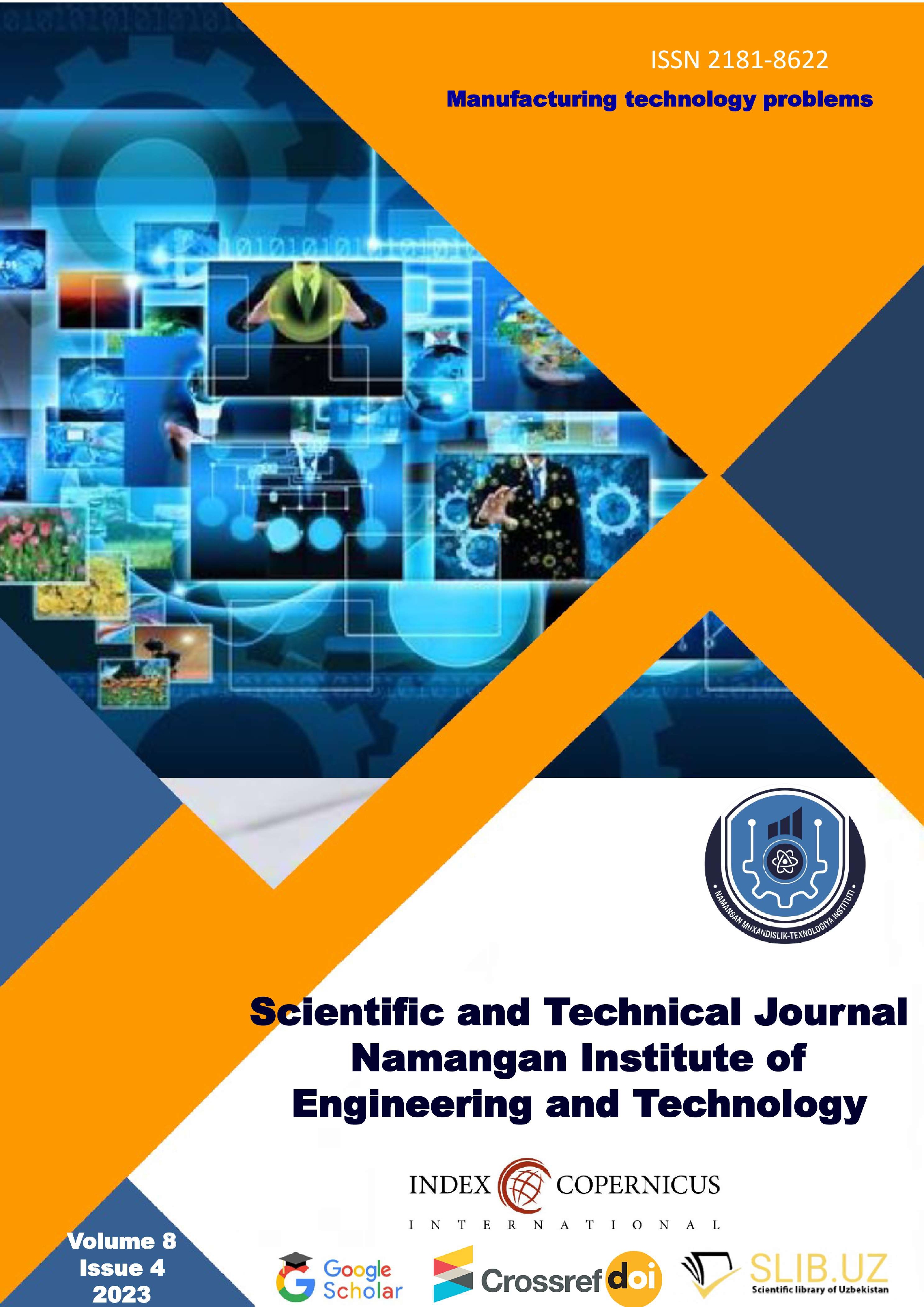